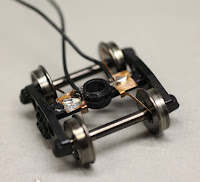
For a demonstration of one of the methods for adapting the springs as pickups, watch our video:
There are two methods for this installation: solder/glue method and drill/screw method.
Solder/Glue Method
Solder wires directly onto the centering springs, then glue the
centering springs to each side of the plastic truck bolster.
Materials
- Kadee No.5 centering springs (2)
- 28 to 32-gauge wire
- Wire strippers
- Wire cutters
- Drill
- 25W soldering iron
- Rosin core solder
- Tweezers
- File
- Modeling glue
- Toothpick
- Heat-shrink tubing
- Heat gun or blow dryer
Installation
- Remove trucks from model and set screws aside.
- Remove wheelsets from trucks; gently spread apart the frame and pull out the axles. Set wheels aside.
- Bend the spring leaves out and away from the each plate with tweezers.
- Using wire cutters, halve each plate so that the side with the attached spring leaves can be used. The side with the hole can be discarded.
- Cut two 4-5” lengths of wire.
- Strip and tin one end of each wire.
- Solder a wire to the center of the topside of each plate.
- Run a file across the top of the plastic bolsters and along the bottom of the metal plate to roughen each surface. This will allow the glue to hold the centering springs to the bolster more securely.
- Approximate the placement of the centering springs to ensure the spring leaves will lightly, but evenly, touch the inside area of each wheel. Do this by matching it up with another set of trucks.
- Use a toothpick to apply glue onto the coarse topsides of the bolster and the bottoms of the plates. Glue the centering springs into place.
- Reinstall the wheelsets after the glue has dried. Ensure the spring leaves are wiping the inside of each wheel and make adjustments as needed. Ensure the spring leaves are not riding the insulating bushing on the axle.
- If necessary, drill two holes in the underframe of the model (one hole for each wire) and thread the wires through the underframe.
- Bend the wires to ensure they will not interfere with the bolster. Screw the trucks back onto the underframe.
- Strip and tin the red SoundCar wire (right rail), black SoundCar wire (left rail), and the remaining ends of the wires.
- Slide a piece of heat-shrink tubing over each wire.
- Solder the red SoundCar wire to the pickup wire for the right rail.
- Solder the black SoundCar wire to the pickup wire for the left rail.
- Slide heat-shrink tubing over the connections and heat with a heat gun or blow dryer to insulate.
Drill/Screw Method
Drill a hole through each side of the bolster and each centering spring, then entwine the stripped end of the wire around a 1-72 sized screw and fasten it through the centering springs and bolsters.
Materials
- Kadee No.5 centering springs (2)
- 28 to 32-gauge wire
- Wire strippers
- Wire cutters
- Tweezers
- Drill, drill bit, and tap
- 0.25”, 1-72 roundhead screws (2)
- Modeling glue
- Toothpick
- Heat-shrink tubing
- Heat gun or blow dryer
- 25W soldering iron
- Rosin core solder
Installation
- Remove trucks from model and set screws aside.
- Remove wheelsets from trucks; gently spread apart the frame and pull out the axles. Set wheels aside.
- Modify the Kadee centering springs (2) so they fit neatly atop each truck bolster and do not cover the screw holes for mounting the trucks.
- Bend the spring leaves out and away from the plate with tweezers.
- Using wire cutters, halve the plate so that the side with the spring leaves attached can be used and the side with the hole can be discarded.
- Drill a hole through the middle of each side of the bolster and a hole through the center of each plate. These holes must be sized to support 1-72 screws. Tap hole for a clean mount.
- Cut two 4-5” lengths of wire.
- Strip one end of each wire about 1”.
- Approximate the placement of the centering springs to ensure the spring leaves will lightly, but evenly, touch the inside area of each wheel. Do this by matching it up with another set of trucks.
- Entwine the stripped end of each wire with each 1-72 sized screw, and fasten them through the holes drilled in the centering springs and bolsters. A wire should now be secured through both centering springs and into each side of the bolster. This will allow a metal-on-metal connection to deliver electricity to the SoundCar.
- Reinstall the wheelsets. Ensure the spring leaves are wiping the inside of each wheel and make adjustments as needed. Ensure the spring leaves are not riding the insulating bushing on the axle.
- If necessary, drill two holes in the underframe of the model (one hole for each wire) and thread the wires through the underframe.
- Bend the wires to ensure they will not interfere with the bolster. Screw the trucks back onto the model.
- Strip and tin the red SoundCar wire (right rail), black SoundCar wire (left rail), and the remaining ends of the wires.
- Slide a piece of heat-shrink tubing over each wire.
- Solder the red SoundCar wire to the pickup wire for the right rail.
- Solder the black SoundCar wire to the pickup wire for the left rail.
- Slide heat-shrink tubing over the connections and heat with a heat gun or blow dryer to insulate.